Carrara for CAD work
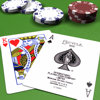
I've been working with Carrara somewhat extensively for design of items to be printed from a 3d printer. Even though it's not primarily a CAD program I find it still has some key advantages over the other packages I've tried. Given that 3d printing is becoming increasingly affordable and popular, I thought I'd list some of my findigs here some the DAZ folk would have a heads up on what they could look into to capture more of that market.
First, why I like Carrara over the other apps: The biggest advantage is the ability to make items semi-transparent, and then edit a polymesh while still having those other items visible. I work on complex parts which have a lot of pieces and I have to make the pieces fit together - so being able to see those other peices means I can very quickly modify my parts to fit without having to do drawings and calculations on the side.
The ability to animate is also very useful. My models have moving parts. The ability to animate the parts is useful in that I can see if any component colides with another. I set up a couple of keyframes, then I model at time 0. When I think it's good, I scroll through the animation to see if any of the objects collide.
Outside of this, Carrara has a very good toolset for doing 3d modelling. Especially for the price.
What Carrara could improve on to make it good for 3d CAD:
1) (key) the ability to tell if a polymesh is good. I've exported my meshes several times to find I was missing a polygon, or that a polygon had a reversed normal. It should be a simple matter to create a check that checks that every edge is attached to exactly two polygons, and that the polygon normals are in the same direction. It would be really nice to be able to highlight any offending edges so I know where to fix.
2) (key) fix up 'Add Thickness' so that it does its offsets from polygons rather than verticies. Right now when you do add thickness or offset surface, it takes the vertex normal, and applies a new vertex a fixed distance from the old one. It should do the same thing, but multiply the distance by a value based on the angle of the edges connected to the vertex (and fail if the angle is close to 180).
3) (key) add STL export -- or even better add gcode/bfb support. 3d printers use gcode, which is generated from STL files. You can get third party software to convert obj to STL, and then use another program to convert STL to gcode but that's a bit of a pain. Reducing the steps is nice.
4) (nicity): add a center-of-gravity calculator, and allow the hot point to be moved to the center of gravity. This would also be very useful in doing regular animations as well, so I'm not sure why it isn't there yet... A simple, way might be to do ray tracing of paralel rays, and calculate the entry/exit point of each ray, put a point in the middle of that line, and then average all the points. It's not guarenteed to be completely accurate, but it would be good enough for practical purposes.
4) (nicity): Add a polymesh primative which is simply a square with circle in the middle of it. Drilling holes in items costs a lot of time, and this would save some (note: using 3d boolean is not good for doing CAD models, because often errors occur, and it adds a lot of unweildly polygons to your mesh).
5) (nicity): Add a keystroke which will align all selected vertexes with the nearest grid point.
6) (nicity, and not just for CAD...) Model with Symmetry: I spent two and a half hours on this the other day trying to ge this to work. I tried googlin for help on using it, I watched a couple of utube vidoes, etc. I finally gave up. I'd want the symetry to be able to automatcally set itself at 0,0,0. Once set, it should automatically be able to detect points which are already symetrical (within a user specified tolerance), and then allow a user to simply use it... There's likely a way to do this, but if I couldn't figure it out in that time, it's not really there.
7) nicity: smaller working box: 20cm x 20 cm x 20cm (which is the biggest most 3d printers support now).
I don't know if the DAZ folk read this forum, so if there's a better place to post/send this, let me know.
John
Comments
Congratulations, John.
You're the first post to make it into the new: Letters to Santa - Carrara development Requests thread in the stickied "Carrara Information" Thread. I've been meaning to start something like this, do this was a perfect start. Great suggestions and nice detailed explanation of what you need.
Jvlur
This Carrara use of is of great interest to me. I done some work in Alibre, Solidworks, and Sketchup.
A matter of fact I'm about to take some college courses in Solidworks.
I'm currently doing technical animation videos. Alibre, or solidworks would really be better software
for creating the type of objects I need, but I have managed to do 95% of the work in Carrara.
From what I've heard around the fourms, and seen myself I believe Hexagon might be a bit closer to my needs
( this is just a guess not a fact), but i'm pretty much steeped in Carrara at the moment.
Anyway nice to see a post on this topic.
8068
Solidworks is pretty darn cool. My pre-Microsoft job was at a metal casting foundry -- one guy there used Solidworks to model the molds and then simulate how the metal would cool and solidify inside. It helped enormously to find problems well in advance of pouring the metal.
Carrara is simply not a tool for this kind of work, and I don't mean that as a criticism, rather, it is intended to be fair. Carrara does A LOT for the money. Asking it to be a true solids modeler however puts it into a category it was never intended for, and could never be supported for its selling price.
Objects like the primitives that enclose volume, or operations like extruding a closed shape, that produce a volume can in some cases be exported successfully from Carrara as a solid (watertight) object when read into 3d printing programs.
However, the more you do to the object, the less likely it will stay a solid. Overlapping, intersecting, and non manifold surfaces can result from many of the modelling operations. Carrara does not care about solids, it only produces surfaces for rendering. It can use booleans, which typically are associated with solid modelers, but it lacks the ability to analyze the result to be sure it is still a solid.
Some tools that can help with 3d printing are:
CADSpan http://www.cadspan.com/
Netfabb Studio http://www.netfabb.com/
Meshlab http://meshlab.sourceforge.net/
CADSpan and Netfabb both have free versions. They also both have time limited free trials of their "Pro" versions.
CADSpan is potentially very useful because it basically retopos the object, so if you have internal overlapping surfaces from multiple objects, it gets rid of those insides as it builds a new "skin" that represents the combined surfaces of all the objects. Unfortunately while it is successful at producing a solid, it may also have "melted" some of the fine details.
Netfabb Studio basic (free) is great. I use it all the time, and have used it extensively with hexagon and booleans. When I get to point that hexagon can no longer boolean an object or do other operations to it, I fix it in netfabb and then bring it back into hexagon for further work. This method probably will work for Carrara as well.
Meshlab is open source, and can be frustrating to to do this kind of repair work. It is also limited in the type of repairs it can make, but it can do some things that Netfabb can't, like rebuilding all the surfaces by reverting it to a point cloud and using its surface functions to generate new ones.
Hope this helps
Carrara is better than Meshlab and sketchup. Never tried the others (that includes hex). There's a bit of getting used to stuff for all programs, and that goes for Carrara to. That being said, I can create/modify a model quite quickly in Carrara's interface. I work in plastic, so cooling, etc doesn't really apply to me (though now that you mention it, ABS warps if you have really long strands of it on the second and third print layers -- don't suppose solidworks has something for that?). I'd post some pictures, but I'm currently working on a product proposal which hasn't been released yet. I can say it's mechanical in nature, and has five moving parts which have to work relative to one another. I was able to design the product quite well on Carrara. I had to do a few redesigns due to friction and stress-factors, and Carrara doesn't provide any support for these, but then again, I've got my own printer, so I can print, test, tweak and reprint easily enough.
John
When I said "melted" I should have clarified that is what CADSpan can do to some of the finer details in the STL file if the settings are not adjusted right, as opposed to melting in the printing process. The geometry can get overly simplified, and it is sometimes difficult to preserve the details and still get a solid. I have not worked with it in a while, so perhaps they have improved it.
CarraraPro v6 had an STL export, but it was taken out in later versions. Not sure why Daz did that that, as STL is a public format did not cost them to license it. Hexagon has STL export but only the ASCII version, which makes huge files.